W Polsce wymagania techniczne dotyczące autoklawizowanych betonów komórkowych są określone przez normy. Normami tymi są PN-07-069, PN-07-059 i PN-65/B-06258. Ciężar objętościowy takich betonów wynosi od 300 do 2000 kg/m3. Wilgotność betonu suchego nie przekracza zazwyczaj 2%. Natomiast, gdy beton określamy jako powietrzno-suchy wynosi od 6 do 8%. W Polsce możemy wyróżnić cztery odmiany betonów komórkowych, które różnią się od siebie swoim ciężarem objętościowym. W naszym kraju najczęściej stosuje się beton odmiany 07. Ciężar objętościowy określany jest jako funkcja porowatości struktury betonu. Zmieniają się one wraz z innymi cechami fizycznymi w zależności od wysokości elementu, która mierzona jest w kierunku wzrostu masy betonowej w formie.[uprawnienia budowlane konstrukcyjno-budowlane]
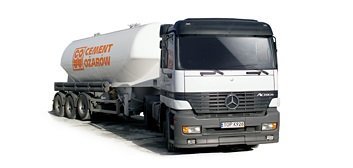
Badanie mrozoodporności
W Rosji zostały przeprowadzone badania przez Makariczewa mrozoodporności betonów komórkowych. Przedstawiono w nich zmianę w wytrzymałości na ściskanie autoklawizowanych betonów komórkowych uzależnioną od liczby cykli zamrażania. Według Makariczewa w badaniach nie zauważono wyraźnej zależności pomiędzy mrozoodpornością betonu, a wartością jego ciężaru objętościowego. Stwierdzenie to różni się jednak od szeroko znanych poglądów.[segregator uprawnienia budowlane]
Odporność na wysokie temperatury
Przeprowadzone zostały również badania, które miały wykazać jaki wpływ mają wysokie temperatury na wytrzymałość betonu cementowego Siporex. Badanie zostało przeprowadzone na kostkach o wymiarach 10×10 centymetrów, które wcześniej zostały wysuszone w temperaturze 110°C. Początkowo podczas wzrastania temperatury wzrastała również wytrzymałość betonu. Po przekroczeniu wartości 400°C wytrzymałość zaczęła spadać. Pierwsze rysy na betonie powstawały już przy temperaturze wynoszącej 225°C. Rysy te nie wpływały jednak na wytrzymałość materiału. Dla temperatury 500°C na wszystkich próbkach były już widoczne rysy, które znacząco obniżały wytrzymałość betonu. W przypadku próbek podgrzewanych do temperatury 400°C początkowo nie zauważa się rys. Pojawiają się one dopiero później podczas ponownego zawilgocenia próbek.[egzamin na uprawnienia budowlane]
Beton lekki belitowy
Beton lekki belitowy oznaczany jest jako BLB. Podczas jego produkcji stosuje się cementy specjalnego typu, które mają zwiększoną zawartość minerałów. Minerałem tym jest belit. Jego zawartość w klinkierach cementów portlandzkich wynosi od 7 do 37%. Według klasyfikacji podanej przez Okorokowa do cementów belitowych możemy zaliczać cementy, w których stosunek ilościowy alitu do belitu wynosi mniej niż jedności. Cement belitowy miał istotny wpływ na rozwój betonów komórkowych w Polsce. Został on zastosowany po raz pierwszy w 1954 roku. Dzięki temu umożliwione zostało znaczne poprawienie jakości produkowanych betonów komórkowych. Dzięki temu do produkcji można również stosować cementy niższych marek oraz wyodrębniona została pierwsza polska technologia dla betonów komórkowych.[akty uprawnienia budowlane]
Surowce stosowane do produkcji BLB
Do produkcji BLB możemy wykorzystywać różne surowce. Są nimi między innymi piasek, w którym zawartość krzemionki powinna wynosić co najmniej 90%. Innym surowcem jest cement belitowy lub hutniczy, który zawiera co najmniej 40% belitu. Kolejnym surowcem jest wapno hydratyzowane. Powinno odznaczać się ono stałą objętością. Możemy spotkać się również z proszkami glinowymi doborowej jakości czy ze środkami powierzchniowo czynnymi w postaci emulsji.
Technologia produkcji BLB
Technologia produkcji BLB obejmuje kilka czynności. Pierwszą z nich jest zmielenie piasku z dodatkiem około 60% wody. Odbywa się to w młynach rurowych. Zmielona postać ma formę szlamu o powierzchni właściwej wynoszącej 1600-2000 cm2/g.[uprawnienia budowlane] Następnie dodaje się do niego około 1-2% Ca(0H)2. Taki szlam jest gromadzony w silosach, które są wyposażone w urządzenia, których zadaniem jest przeciwdziałanie sedymentacji. Dojrzały szlam jest dokładnie odmierzany i podgrzewany do temperatury 40-50°C. Następnie wlewa się go do szczelnej mieszarki szybkobieżnej. Do tej samej mieszarki wsypuje się dokładnie odważony cement belitowy. Kolejnym etapem jest dokładnie mieszanie, które trwa 3-5 minut. Kolejno do mieszarki dodawana jest emulsja o działaniu powierzchniowo-czynnym i proszek glinowy. Proszek ten ma postać zawiesiny lub pasty. Następnie całą mieszaninę się dokładnie miesza przez około minutę. Ostatnim etapem jest wylanie masy do form stalowych, które muszą wcześniej zostać posmarowane smarem, który zapobiega późniejszemu przywieraniu betony do dna i boków formy.[uprawnienia budowlane testy]