Wyróżnia się dwa podstawowe sposoby produkcji podkładów żelbetowych (program na uprawnienia budowlane). Różnią się one od siebie jedynie sposobem rozformowywania podkładów. W przypadku pierwszej metody stosuje się formy pojedyncze, a w przypadku drugiej – formy bateryjne na 8-10 sztuk. Do produkcji wykorzystuje się specjalne przesuwne agregaty bądź formy kroczące.
Proces sprężania jest podstawową czynnością. Jego sposób wpływa bezpośrednio na wybór metody cyklu produkcyjnego. Wyróżnia się dwie podstawowe metody:
– torów długich,
– ruchomych form.
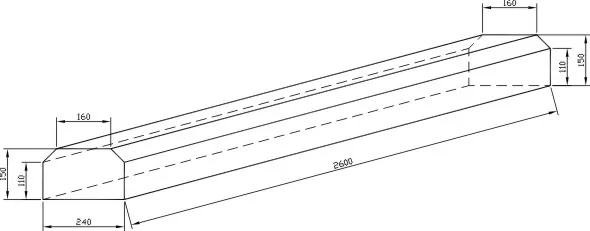
Metoda torów długich
Metoda torów długich opiera się na długim torze naciągowym, który ma powyżej 100 m. Na jego końcach należy zamontować opory do naciągu strun. Jednocześnie należy pamiętać o tym, że formy muszą pozostać nieruchome. Praktycznie cała produkcja odbywa się przy użyciu ruchomych agregatów oraz przesuwanych zasobników.
Proces technologiczny w powyższej metodzie wygląda następująco:
a) przygotowanie form,
b) przygotowanie wiązek zbrojenia i ułożenie ich w formach,
c) naciąganie zbrojenia,
d) napełnianie form betonem,
e) zagęszczanie betonu,
f) dojrzewanie betonu (połączone z naparzaniem),
g) sprężanie podkładów (zwalnianie naciągu),
h) przecinanie zbrojenia i rozformowywanie.
Metoda ruchomych form
Cechą charakterystyczną metody ruchomych form jest to, że forma do podkładów przemieszcza się po wcześniej określonej linii technologicznej. Jednocześnie wyróżnia się dwie odmiany produkcyjne (akty prawne do egzaminu na uprawnienia budowlane).
W pierwszej z nich naciąg ma miejsce przed samym procesem betonowania. Forma pełni również funkcję opory naciągowej. Proces technologiczny zakłada cały cykl produkcyjny w formie, która do końca produkcji złączona jest z podkładem. Z kolei operacje technologiczne są zbliżone do tych, które mają miejsce przy metodzie długich torów.
Z kolei w drugim przypadku zakłada się, że sprężenie podkładu ma miejsce dopiero wtedy, kiedy beton osiągnie żądaną wytrzymałość po rozformowaniu. Dzięki temu można uzyskać lepszy obrót form. Jednak operacje technologiczne są inne od tych, które wspomniano wcześniej. Wygląda to następująco:
a) przygotowanie formy i założenie prętów dla wyrobienia kanałów naciągowych w betonie,
b) napełnienie formy betonem,
c) zagęszczenie betonu,
d) rozformowanie i usunięcie prętów,
e) dojrzewanie betonu,
f) założenie zbrojenia w kanały i sprężenie.
Cykl produkcyjny trwa od 12 do 18 godzin przy stosowaniu naparzania w parze bądź wodzie, których temperatura wynosi od 60° do 80°C. Wydajność mieści się na poziomie od 100 000 do 300 000 sztuk rocznie przy założeniu, że pracochłonność na wykonanie 1 podkładu wynosi 0,8-1,2 roboczogodziny.
Badanie podkładu
Podkłady, które są wykonane podlegają systematycznemu badaniu (materiały do egzaminu na uprawnienia budowlane). Podczas takiego badania sprawda się przede wszystkim:
– wygląd zewnętrzny,
– wymiary,
– wytrzymałość na powstawanie rys.
Taki podkład należy zbadać w części podszynowej. Dobry podkład charakteryzuje się tym, że wytrzymuje obciążenie na poziomie 22-30 ton. Wszystko zależy od klasy kwalifikowanej (I klasa 25-30 T, II klasa 22-25 T). Dopuszcza się jednak tolerancję obciążeniową w granicach wyżej wymienionych klas. Należy pamiętać o tym, że wymiary podkładów sprawdza się dla 5% produkcji, wytrzymałość dla 1%.
Charakterystyka toru klasycznego i sztywnego
Tor klasyczny zbudowany jest z szyn, które leżą na poprzecznych równoległych podkładach w pewnych odstępach. Jest to układ, który jest bardzo odkształcalny w płaszczyźnie poziomej. Jednocześnie można go traktować jako ustrój ramowy o węzłach odkształcalnych, które leżą na podłożu sprężystym.
Aby móc zmniejszyć odkształcalność toru w planie, powinno się zadbać o jego usztywnienie, a także zwiększenie stabilności. Jest to możliwe wtedy, kiedy wprowadzi się ustroje kratowe bądź płytowe (szczegółowy program egzaminu na uprawnienia architektoniczne). Jednocześnie ustroje kratowe mogą być:
– płytami małowymiarowymi, które zastępują poszczególne podkłady belkowe,
– płytami monolitycznymi, które są podłożem betonowym toru.