Obciążenie ciężarem własnym
Na konstrukcję grodzi kafarowej nie ma wpływu mechaniczne obciążenie ciężarem własnym czy parcie wiatru. Są to obciążenia drugorzędne. Ze względu na to, że w przypadku tego zagadnienia występuje duża częstotliwość i przypadkowość działania sił, to nie można tego ująć w sposób rachunkowy. Z tego też powodu przyjęto wytyczne konstrukcyjne, które aktualizowano w trakcie uzyskiwania nowych informacji z doświadczeń (uprawnienia budowlane 2021).
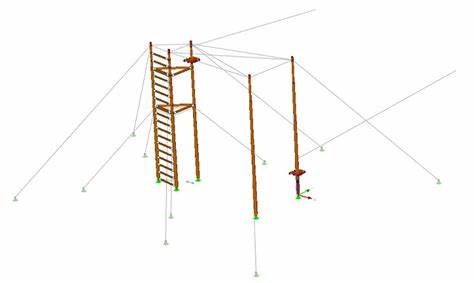
Została przyjęta ogólna zasada, która miała zapobiegać miejscowym wpływom przy pomocy stosowania elementów osłonowych. Podwieszane one były na ścianach grodzi. Elementy te wytrącały częściowo energię kinetyczną odłamków (ugięcie płyt zawieszonych) i jednocześnie rozkładały siły na większe powierzchnie. Używano wtedy swobodnie podwieszanych starych podkładów kolejowych, które później zastąpiono cięższymi balami drewnianymi.
Przeznaczenie blach
Im bardziej rosły wielkości jednostek kafarowych, tym bardziej takie rozwiązania nie były wystarczające. Postanowiono wówczas, żeby wykorzystywać stalowe blachy, których grubość wynosiła 40 mm. Chroniły one dodatkowo dolne pasy grodzi poprzez skośne ustawianie spodków wlewnicowych lub wlewków. Nie było to zbyt bezpieczne rozwiązanie. Liczba odłamków, które były poza obrębem grodzi, znacznie urosła (testy 2021 uprawnienia).
Dlatego też zostały wyeliminowane wszystkie inne osłony i skupiono się tylko na stosowaniu zawieszanych blach. Z kolei grubość blach osłonowych musiała zostać zwiększona ze względu na wyeliminowanie spodków wlewniczych w dolnym pasie grodzi.
Aktualnie używa się blach, które mają grubość 100 mm. Zaobserwowano, że są one wystarczającym materiałem, który jednocześnie jest pewne. Duża bezwładność , a co za tym idzie – duża masa konstrukcji, może zapewnić ogólną wytrzymałość obudowy. Szkielety stalowe nie pełniły swojej funkcji dobrze. Szybko pękały spoiny, a połączenia nitowane ulegały ścinaniu. Na początku szkielety stalowe bywały pokryte betonem. Jednak to rozwiązanie nie należało do trwałych, ponieważ beton pękał i kruszał. Kolejnym etapem było wprowadzenie zbrojenia, które stosowano na obetonowany szkielet. Zrobiono również próbę i wykonano szkielet żelbetowy, który był wypełniony żelbetowymi dylami prefabrykowanymi. Jednak nie było to dobre rozwiązanie. Konstrukcja ta szybciej się uszkadzała (program przygotowujący do uprawnień budowlanych).
Monolityczne grodzie żelbetowe
W dzisiejszych czasach w 99% używa się tylko i wyłącznie monolitycznych grodzi żelbetowych, które są grube. Zbroi się je stalą żebrowaną, która charakteryzuje się niskim Qr i średnimi grubościami w trzech warstwach związanych prostopadłymi strzemionami szpilkowymi. Używa się do tego siatki zbrojeniowej jednakowej, która ma kilkunastocentymetrowe oka (ok. 15 cm). Z kolei w omawianych przypadkach użyto ok. 45 kg stali na 1 m3 betonu.
Taka konstrukcja charakteryzuje się dużą trwałością i odpornością. Wszystko jest dopasowane do charakteru obciążeń. Kafarownie, które podobnie wybudowano, mają wysokie wskaźniki eksploatacyjne. Często eliminują one przestoje, które mogą wyniknąć z remontów grodzi kafarowych.
Plastyczna przeróbka metalu jest podstawowym procesem technologicznym w hutnictwie. Można rozróżnić kilka sposobów takiej przeróbki. Mowa o:
– walcowaniu,
– kuciu,
– prasowaniu,
– przeciąganiu.
Walcowanie należy w tej chwili do najchętniej wybieranego rozwiązania. W krótkim czasie otrzymuje się z dużej bryły stali (z wlewka) profil, który można od razu zastosować w konstrukcji. Dzięki metodzie walcowania powstaje ok. 95% wyrobów stalowych hutnictwa. Są to m.in. kęsy, pręty o różnych profilach, kształtowniki, rury, płaskowniki, blachy grube i cienkie, taśma czy drut. Walcownia jest wydziałem produkcyjnym huty, gdzie dochodzi do procesu walcowania. Są tam maszyny i urządzenia hutnicze, dzięki którym możliwe są odkształcenia plastyczne przez zgniatanie metalu między obracającymi się walcami (program z aktami na uprawnienia budowlane).
Proces walcowania z reguły odbywa się w dwóch temperaturach walcowanego materiału:
- Ok. 1000°C – w walcowniach gorących,
- do 600° – w walcowniach zimnych.